ATACO Steel Products Corporation is a leader in metal components manufacturing. As a progressive, customer-focused company, we’re continually investing in equipment upgrades to maximize product quality while keeping pricing competitive. Our latest investment in the TRUMPF TruBend 5130 press brake not only delivers more accurate repeatability, it improves safety and turnaround times as well.
TRUMPF 5130 TruBend Capabilities & Innovations
TruBend machines have a global reputation for high productivity of quality finished parts. As their most popular press brake, the 5130 model sports plenty of time-and-cost-saving features, including:
- Widest possible machine range accommodates any component geometry
- 6-axis backgauge systems ensure precise positioning
- Thickness Controlled Bending function compensates for variations in sheet thickness
- Automatic tool clamping & automatic bend guards reduce setup time
- ACB Laser automatic angle measuring system records in real-time for fast, precise bends
- Part Indicator simplifies insertion process & reduces rejects
- Touchpoint TruBend interface is as simple and intuitive as using a tablet
- TecZone Bend programming software automatically generates programs based on input data
- On-Demand Servo Drive improves efficiency by only running hydraulics during the bending process. Servo drive also supports hydraulics when pressing large depths
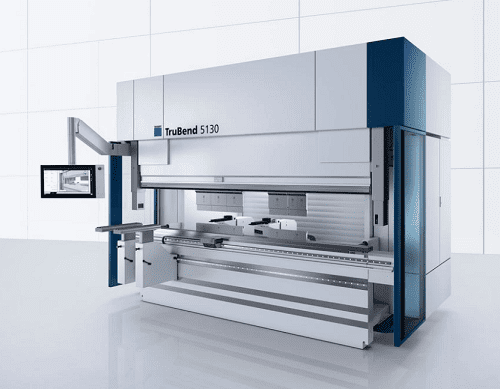
The TruBend Series 5000 is TRUMPF’s most successful bending machine worldwide. Image courtesy of manufacturer.
As one of the world’s leading manufacturers of machine tools for decades, TRUMPF is known for its truly innovative equipment that makes the operator’s job easier. They also offer online training, consultation, and software products.
Brian Petrowsky, Senior Manufacturing Engineer and Maintenance Manager here at ATACO, keeps a close eye on the used equipment market. He sees plenty of press brakes made by other manufacturers turning up for sale all the time, but rarely TRUMPF machines. Investing in a top-of-its-class press brake resonates with our commitment to technological advancement and efficiency. Working with the most advanced and efficient machinery also means better part costs for our customers.
As Brian puts it, “Safety is #1 around here.” The TruBend 5130 has automatic laser light curtains at the ends of the brake that adjust automatically, giving a huge boost to operator safety.
Other key benefits include:
Repeatability. Repeatability. Repeatability. Increased accuracy and consistency in production is everything. This machine actually measures the angle of the part while bending, so there’s no need to stop and re-measure to make sure it’s within tolerance.
Faster turnaround times. Quicker production facilitated by higher working speeds and automatic tool changes saves everyone time and money. A graphical, user-friendly interface reduces time spent setting up.
More capabilities. Using the TRUMPF 5130 TruBend, ATACO can now perform different types of forming, such as roll forming for large radius parts. Short flanges, moldings and holes near the bending line can be accomplished without deformation.
Better bending, better fabrication. A better brake press produces metal parts with greater consistency, which makes all subsequent services more successful. More consistent parts mean more perfectly placed paths in robotic welding and other automated processes.
The TRUMPF 5130 is only the latest example of ATACO Steel’s commitment to utilizing cutting-edge equipment to stay ahead of the competition. Earlier this year we acquired a TRUMPF TruLaser 5030, a high-speed laser cutter with outstanding quality and efficiency. Last year we added a 50-ton servo electric brake press to our fleet. Our earlier acquisition of metal forming simulation software allows our engineers to more quickly evaluate the feasibility of complex parts and processes.
This level of investment not only benefits ATACO’s clients, but our employees, too. As Brian explains, “Associates on the production floor are getting more involved from the start. Learning how to program, setup, and operate the equipment. We tend to provide more training and development than other companies. So operators are really becoming technicians, capable of doing everything from programming to troubleshooting and maintenance.”
Empowering employees to work more safely and expand their skillset is an investment that pays dividends in the form of quality products, a strong company culture, and long-term customer relationships.
Precision Metal Stamping Coast to Coast
Headquartered near Milwaukee, Wisconsin, ATACO Steel delivers the highest quality formed metal parts to manufacturers nationwide.
Request a quote today or contact us to speak to a team member about your project. We look forward to exceeding your expectations and earning your trust.